Category Archives: Operations
Conducting Operational Risk Assessments Effectively
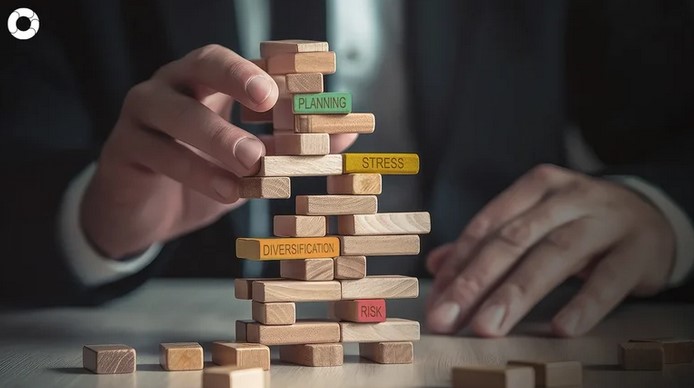
Source:https://www.piranirisk.com
In today’s dynamic business environment, organizations face a wide array of risks that can potentially disrupt operations, impact financial stability, and damage reputations. Conducting an operational risk assessment is crucial for identifying, evaluating, and mitigating these risks before they escalate into significant issues. Whether a company is navigating the challenges of cybersecurity, regulatory changes, or supply chain disruptions, an effective operational risk assessment process helps organizations anticipate potential obstacles and take proactive measures. In this article, we will discuss the importance of operational risk assessments, the steps involved in conducting them effectively, and best practices that can enhance the risk management process.
Understanding Operational Risk Assessment
An operational risk assessment is the systematic process of identifying, analyzing, and evaluating risks that may affect an organization’s day-to-day operations. These risks can arise from various internal and external factors, such as human error, technological failures, process inefficiencies, or environmental events. The goal of the assessment is to prioritize these risks based on their potential impact on the business and to implement mitigation strategies to minimize or eliminate them.
While operational risk assessments are a key component of broader enterprise risk management (ERM) frameworks, they focus specifically on risks associated with the operational aspects of a business, such as workflow, systems, and resources. A well-conducted operational risk assessment allows businesses to create contingency plans, ensure compliance, and improve overall operational resilience.
Steps for Conducting an Effective Operational Risk Assessment
To conduct an operational risk assessment effectively, organizations must follow a structured process that ensures all risks are properly identified, analyzed, and mitigated. Here are the key steps involved:
1. Identify Risks
The first step in any operational risk assessment is to identify the risks that could potentially affect the organization. This involves gathering input from various stakeholders, such as department heads, employees, and even external experts, to ensure that all areas of the business are covered. Common sources of operational risks include:
- Human Factors: Mistakes, lack of training, or employee turnover can introduce risks to operations.
- Technology Failures: Cyberattacks, software bugs, or system outages can disrupt day-to-day operations.
- Process Inefficiencies: Bottlenecks, outdated workflows, or inadequate processes may create operational vulnerabilities.
- External Factors: Supply chain disruptions, regulatory changes, or natural disasters are examples of external risks that need to be considered.
Using tools such as brainstorming sessions, surveys, and historical data analysis can help ensure that all potential risks are identified.
2. Assess and Analyze Risks
Once risks are identified, the next step is to assess and analyze them. This phase involves determining the likelihood of each risk occurring and its potential impact on the organization. Organizations typically use qualitative or quantitative methods to assess risks. Some common techniques include:
- Risk Matrix: A visual representation that helps assess the likelihood and impact of risks on a scale (e.g., low, medium, high). This method helps prioritize which risks need immediate attention.
- Failure Mode and Effects Analysis (FMEA): A systematic approach to identifying potential failure modes in processes and their consequences, helping to prioritize actions.
- Quantitative Models: These models use data and statistical methods to measure the probability of risks and their financial impacts.
By evaluating the risks in this manner, organizations can better understand which risks are most critical and require immediate action versus those that can be monitored over time.
3. Develop Mitigation Strategies
After assessing the risks, organizations need to develop strategies to mitigate or reduce the impact of these risks. Risk mitigation strategies can include:
- Process Improvements: Streamlining workflows and procedures to reduce inefficiencies and errors.
- Technology Upgrades: Implementing more secure, reliable, or efficient technology to prevent system failures or breaches.
- Training Programs: Providing regular training to employees to ensure they are prepared to handle potential operational disruptions.
- Contingency Plans: Developing backup plans, such as alternative suppliers or disaster recovery strategies, to ensure business continuity in the face of disruptions.
Risk mitigation should aim to either reduce the likelihood of the risk occurring or lessen its impact on the business if it does happen. The strategies should be tailored to the specific needs and circumstances of the organization.
4. Implement and Monitor the Action Plan
Once the mitigation strategies are developed, they must be implemented effectively. This phase requires collaboration across departments to ensure that action plans are carried out efficiently. Communication is key during implementation, as stakeholders must be informed of their roles in the process and the timeline for execution.
After implementing the mitigation strategies, it is essential to continuously monitor the effectiveness of the actions taken. Monitoring allows the organization to identify if further adjustments are necessary or if new risks have emerged that require attention. This can be done through regular reviews, performance metrics, and feedback from employees involved in the day-to-day operations.
5. Review and Update the Risk Assessment
An operational risk assessment should not be a one-time event. As business environments, technologies, and processes evolve, new risks can emerge. Therefore, it is important to periodically review and update the risk assessment to ensure that it remains relevant and accurate. This ongoing process helps organizations stay agile and responsive to potential threats, enabling them to adapt their risk management strategies as needed.
Best Practices for Conducting Operational Risk Assessments
To ensure that your operational risk assessment is effective and yields actionable results, consider the following best practices:
1. Engage All Relevant Stakeholders
Operational risk assessments should involve input from all relevant stakeholders, including employees, department heads, risk managers, and even external partners. This collaborative approach ensures that all potential risks are identified and addressed, and it fosters a culture of shared responsibility for risk management.
2. Leverage Technology and Data
Modern technology can greatly enhance the risk assessment process. Using advanced data analytics tools, risk management software, and automated systems can help identify and analyze risks more efficiently. These tools can provide real-time insights into potential risks and track the effectiveness of mitigation efforts over time.
3. Establish a Risk Management Framework
A well-defined risk management framework is essential for ensuring that the operational risk assessment process is structured, consistent, and aligned with organizational objectives. This framework should outline the steps involved, the roles and responsibilities of stakeholders, and the criteria for assessing and prioritizing risks.
4. Foster a Risk-Aware Culture
Creating a risk-aware culture is key to the success of any risk assessment process. Encourage employees at all levels to report potential risks and contribute to risk mitigation efforts. This proactive approach helps create an environment where risks are identified early, and actions are taken swiftly to address them.
In conclusion, conducting an operational risk assessment is an essential step in managing the potential risks that could disrupt an organization’s operations. By following a structured process that includes risk identification, assessment, mitigation, and ongoing monitoring, businesses can not only reduce the likelihood of operational disruptions but also ensure continuity and resilience in the face of unforeseen challenges. An effective operational risk assessment can help organizations navigate an increasingly complex and unpredictable environment, making it a critical component of any comprehensive risk management strategy.
Supply Chain Resilience: Navigating Disruptions in Modern Operations
Supply chain resilience is a critical component of modern operations. It is the ability of a supply chain to respond to disruptions and maintain operations in the face of unexpected events. Supply chain resilience is essential for businesses to remain competitive in today’s rapidly changing environment. It requires a comprehensive understanding of the supply chain, its components, and the potential risks associated with it. This understanding must be combined with the right strategies and tools to ensure that the supply chain is able to respond quickly and effectively to disruptions. By understanding the importance of supply chain resilience and how to navigate disruptions, businesses can ensure that their operations remain efficient and profitable.
How to Leverage Technology to Enhance Supply Chain Resilience in the Face of Disruptions
In today’s globalized economy, supply chain disruptions can have a significant impact on businesses. To ensure supply chain resilience in the face of disruptions, organizations must leverage technology to create a more agile and responsive supply chain.
One way to leverage technology to enhance supply chain resilience is to use predictive analytics. Predictive analytics can help organizations anticipate potential disruptions and take proactive steps to mitigate their impact. For example, predictive analytics can be used to identify potential supply chain bottlenecks and take steps to address them before they become a problem. Additionally, predictive analytics can be used to identify potential risks and develop strategies to mitigate them.
Another way to leverage technology to enhance supply chain resilience is to use automation. Automation can help organizations streamline their supply chain processes, making them more efficient and responsive. Automation can also help organizations reduce costs and improve customer service. Additionally, automation can help organizations quickly respond to disruptions by quickly rerouting shipments and adjusting production schedules.
Finally, organizations can leverage technology to improve visibility into their supply chain. By using real-time tracking and monitoring tools, organizations can gain a better understanding of their supply chain and quickly identify potential disruptions. This improved visibility can help organizations take proactive steps to mitigate the impact of disruptions and ensure supply chain resilience.
By leveraging technology to create a more agile and responsive supply chain, organizations can ensure supply chain resilience in the face of disruptions. Predictive analytics, automation, and improved visibility can all help organizations create a more resilient supply chain and mitigate the impact of disruptions.
Strategies for Building a Robust Supply Chain Resilience Plan to Mitigate Disruptions
1. Establish a Risk Management Plan: Develop a comprehensive risk management plan that identifies potential risks and outlines strategies to mitigate them. This plan should include a risk assessment of the entire supply chain, from suppliers to customers, and should be regularly updated to reflect changes in the market.
2. Develop a Contingency Plan: Develop a contingency plan that outlines how the organization will respond to disruptions in the supply chain. This plan should include strategies for dealing with supply chain disruptions, such as alternative suppliers, alternative transportation routes, and alternative production methods.
3. Utilize Technology: Utilize technology to monitor the supply chain and identify potential risks. This includes using predictive analytics to anticipate disruptions and using real-time data to monitor the supply chain.
4. Establish Partnerships: Establish partnerships with suppliers and other stakeholders in the supply chain to ensure that the organization is prepared for potential disruptions. This includes developing relationships with alternative suppliers and transportation providers.
5. Invest in Training: Invest in training for employees to ensure that they are prepared to respond to supply chain disruptions. This includes training on how to identify potential risks and how to respond to them.
6. Monitor the Market: Monitor the market for potential risks and disruptions. This includes monitoring the political and economic environment, as well as changes in the industry.
7. Implement Quality Control: Implement quality control measures to ensure that the organization is receiving the highest quality products and services from its suppliers. This includes conducting regular audits of suppliers and their processes.
8. Establish Communication Protocols: Establish communication protocols to ensure that all stakeholders in the supply chain are informed of potential risks and disruptions. This includes developing a communication plan that outlines how information will be shared and who will be responsible for sharing it.
Conclusion
In conclusion, supply chain resilience is an essential component of modern operations. It is important for organizations to be prepared for disruptions and to have a plan in place to ensure that their supply chain remains resilient. By understanding the risks associated with supply chain disruptions, organizations can develop strategies to mitigate those risks and ensure that their supply chain remains resilient. Additionally, organizations should take advantage of technology and data analytics to gain insights into their supply chain and identify potential disruptions before they occur. By taking these steps, organizations can ensure that their supply chain remains resilient and can navigate disruptions in modern operations.
Operational Efficiency Redefined: Streamlining Your Business for Growth
Operational Efficiency Redefined: Streamlining Your Business for Growth is a comprehensive guide to improving the efficiency of your business operations. It provides a comprehensive overview of the key elements of operational efficiency, from process optimization to resource management. It also provides practical advice on how to identify and address inefficiencies in your business operations, as well as how to use technology to improve efficiency. This book is an invaluable resource for business owners and managers who want to maximize their operational efficiency and drive growth.
How to Leverage Automation to Improve Operational Efficiency
Automation is a powerful tool that can be used to improve operational efficiency. Automation can help streamline processes, reduce costs, and increase productivity. By leveraging automation, businesses can reduce manual labor, eliminate errors, and improve customer service.
Automation can be used to automate repetitive tasks, such as data entry, customer service, and order processing. Automation can also be used to automate complex processes, such as inventory management, financial reporting, and customer relationship management. Automation can also be used to automate customer service, such as responding to customer inquiries and providing customer support.
Automation can also be used to improve operational efficiency by reducing manual labor. Automation can be used to automate mundane tasks, such as data entry and customer service, freeing up employees to focus on more important tasks. Automation can also be used to automate complex processes, such as inventory management and financial reporting, reducing the amount of time and effort required to complete these tasks.
Automation can also be used to reduce errors and improve customer service. Automation can be used to automate customer service tasks, such as responding to customer inquiries and providing customer support. Automation can also be used to automate complex processes, such as inventory management and financial reporting, reducing the chances of errors.
Finally, automation can be used to improve operational efficiency by increasing productivity. Automation can be used to automate mundane tasks, such as data entry and customer service, freeing up employees to focus on more important tasks. Automation can also be used to automate complex processes, such as inventory management and financial reporting, reducing the amount of time and effort required to complete these tasks.
In conclusion, automation is a powerful tool that can be used to improve operational efficiency. Automation can be used to automate mundane tasks, such as data entry and customer service, freeing up employees to focus on more important tasks. Automation can also be used to automate complex processes, such as inventory management and financial reporting, reducing the amount of time and effort required to complete these tasks. Automation can also be used to reduce errors and improve customer service. By leveraging automation, businesses can reduce manual labor, eliminate errors, and improve customer service.
The Benefits of Investing in Operational Efficiency for Business Growth
Investing in operational efficiency is an important step for businesses looking to grow and succeed. By streamlining processes and improving efficiency, businesses can reduce costs, increase productivity, and improve customer satisfaction. Here are some of the key benefits of investing in operational efficiency for business growth.
First, investing in operational efficiency can help businesses reduce costs. By streamlining processes and eliminating unnecessary steps, businesses can save money on labor, materials, and other resources. This can help businesses reduce overhead costs and increase their bottom line.
Second, investing in operational efficiency can help businesses increase productivity. By streamlining processes and eliminating unnecessary steps, businesses can reduce the amount of time it takes to complete tasks. This can help businesses increase their output and improve their overall efficiency.
Third, investing in operational efficiency can help businesses improve customer satisfaction. By streamlining processes and eliminating unnecessary steps, businesses can reduce the amount of time it takes to complete tasks. This can help businesses provide better customer service and improve customer satisfaction.
Finally, investing in operational efficiency can help businesses increase their competitive advantage. By streamlining processes and eliminating unnecessary steps, businesses can reduce the amount of time it takes to complete tasks. This can help businesses stay ahead of the competition and gain a competitive edge.
In conclusion, investing in operational efficiency is an important step for businesses looking to grow and succeed. By streamlining processes and improving efficiency, businesses can reduce costs, increase productivity, and improve customer satisfaction. This can help businesses increase their competitive advantage and achieve long-term success.
Conclusion
Operational Efficiency Redefined: Streamlining Your Business for Growth provides a comprehensive guide to improving operational efficiency and driving business growth. By understanding the key components of operational efficiency, businesses can identify areas of improvement and develop strategies to increase efficiency and reduce costs. With the right tools and processes in place, businesses can create a more efficient and profitable organization that is better positioned for long-term success.